Interview with Fujiya Sakuma,
a Japanese potter in MashikoTown
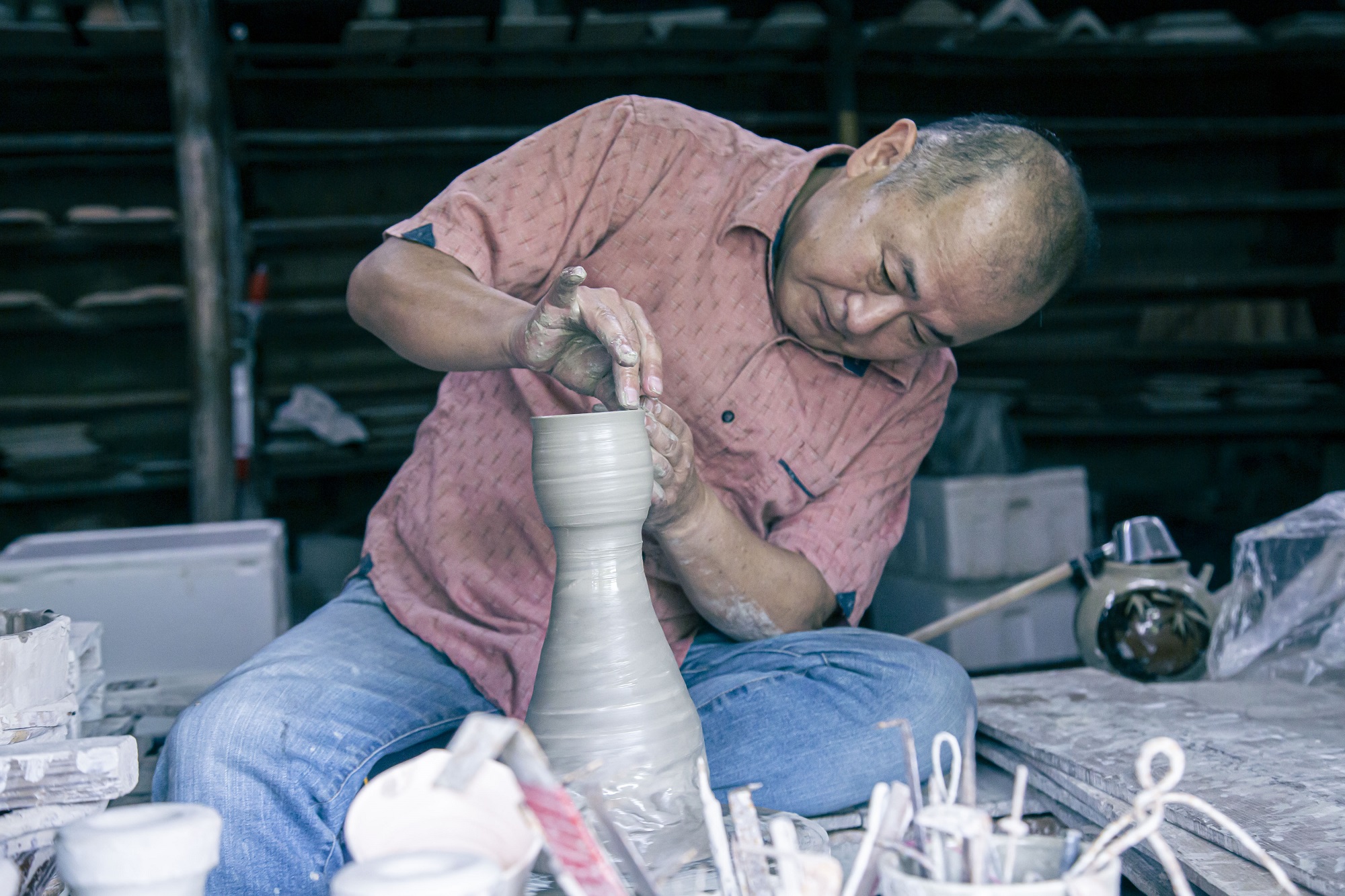
Shoji Hamada (1894~1978) was a potter who had elevated Mashiko ware from everyday tableware to works of art that people would display in their alcove.
Fujiya Sakuma is the grandson of Totaru Sakuma (1900~1976), who had extensive contact with Shoji Hamada.
We spoke to Fujiya Sakuma, who continues to make original products in Mashiko even today, on what had inspired him to become a potter and about Mashiko ware in general.
Blessed with an open-minded culture,
Mashiko is now home to the creative activities of over 200 potters.
Take a look at this pot. It was made by allowing the white glaze to flow down as it is guided by the pattern. Normally, the glaze would flow straight down due to the force of gravity, and if this white part trickles all the way to the bottom, it would make the pot look sloppy. However, people in the past did not create grooves in their pottery, and they simply let the glaze trickle down. Of course, the shape of pottery is important, but the way in which the glaze is applied is also fascinating because everyone has their own unique style of doing it.
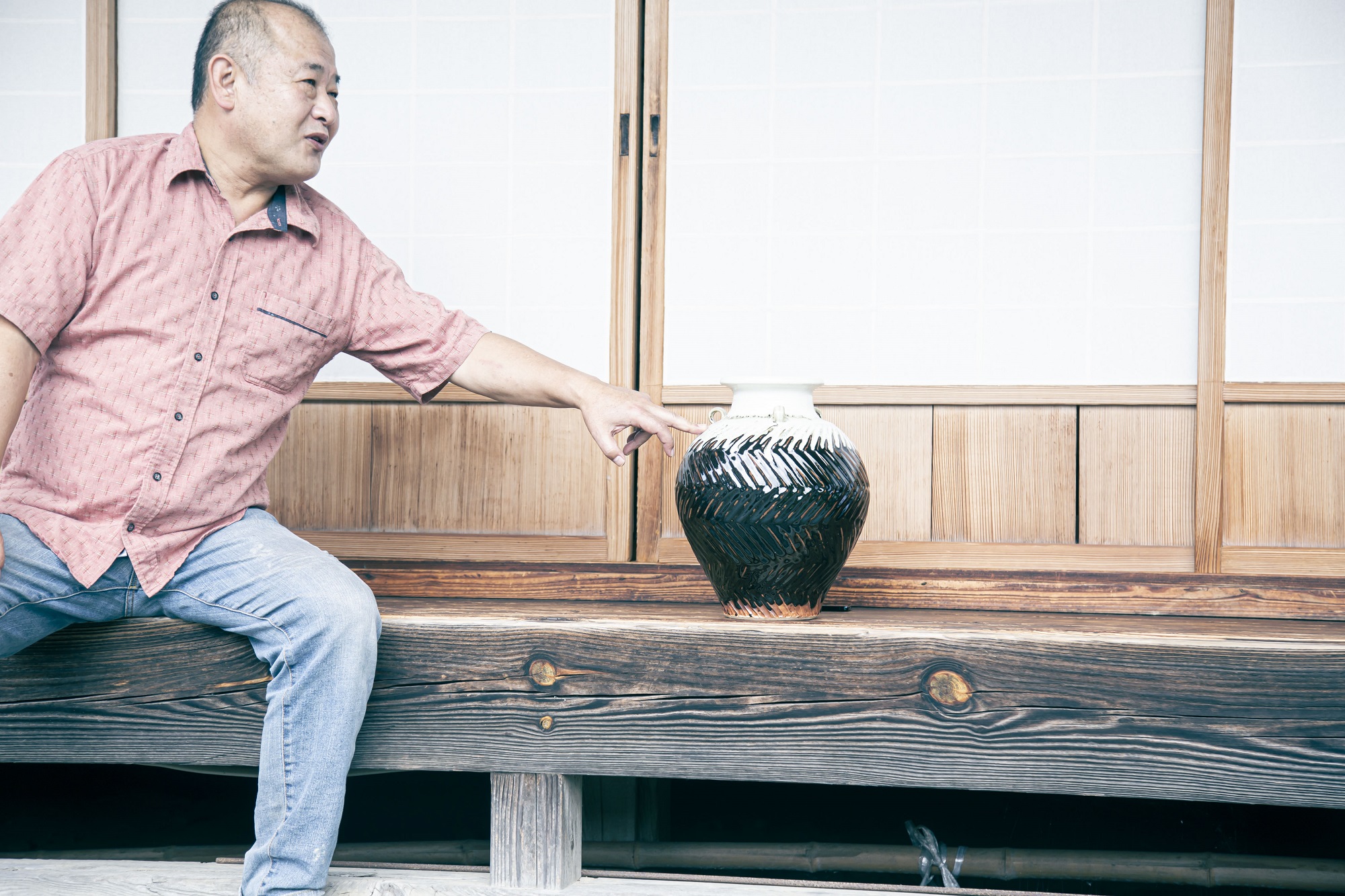
―――What inspired you to become a potter?
Sakuma: My family has been potters for generations, so naturally, I often come into contact with ceramics ever since I was a child. My grandfather would give me pocket money whenever I brought pottery shaped like animals such as cats and dogs to his place (laughs). I was delighted with the money he gave me, so I made all kinds of different things.My grandfather, Totaro Sakuma (1900~1976), made Mashiko ware at a kiln that his father had built. He was strongly drawn to Shoji Hamada-sensei (1894~1978), now regarded as a national living treasure, during Hamada-sensei’s visit to Mashiko one day. He would invite Hamada-sensei to his house and work alongside him after his daily shift was over. Hamada-sensei used to stay over and sleep in this spot where I am sitting right now.Before I realized, my grandfather had truly inspired me and set me on the path of becoming a potter. I went to an art university for college. But to be honest, I still had some doubts at that time about becoming a potter.
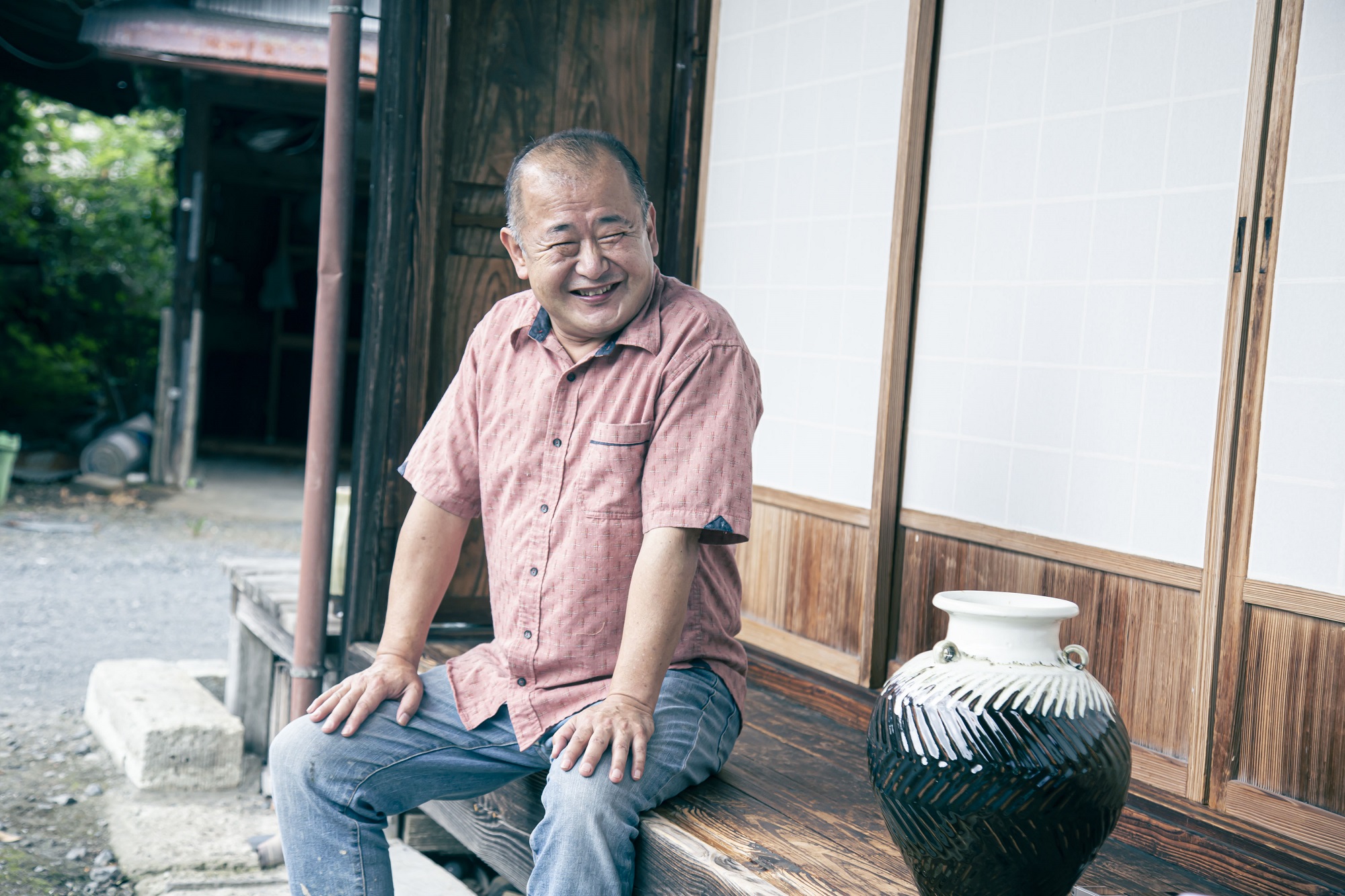
―――So even as a university student, you had doubts about becoming a potter?
Sakuma: My father, who had inherited my grandfather’s craft, passed away suddenly when I was in my fourth year of college. We had hired a craftsman at the kiln at the time. I could not afford to hesitate under such circumstances, so I naturally decided to take over. After graduating from university, I joined a training institute and was determined to learn how to make Mashiko pottery. I returned to the kiln in my hometown a year later and asked the craftsman what I should make, and I was told to replicate teacups using a sample I was handed. I made around 20 teacups that day, and I showed them to the craftsman. He told me to put them directly into the clay kneader so that I can use them again tomorrow. In other words, none of them was up to par, and I had to break them down into clay again. Clearly, what I had learned in school could not be directly applied to the professional world of pottery. I was so frustrated by this that I continued to practice my craft diligently every day after that. I only left the potter’s wheel when I needed to use the restroom. On some days, I made as many as 400 teacups in a single day.
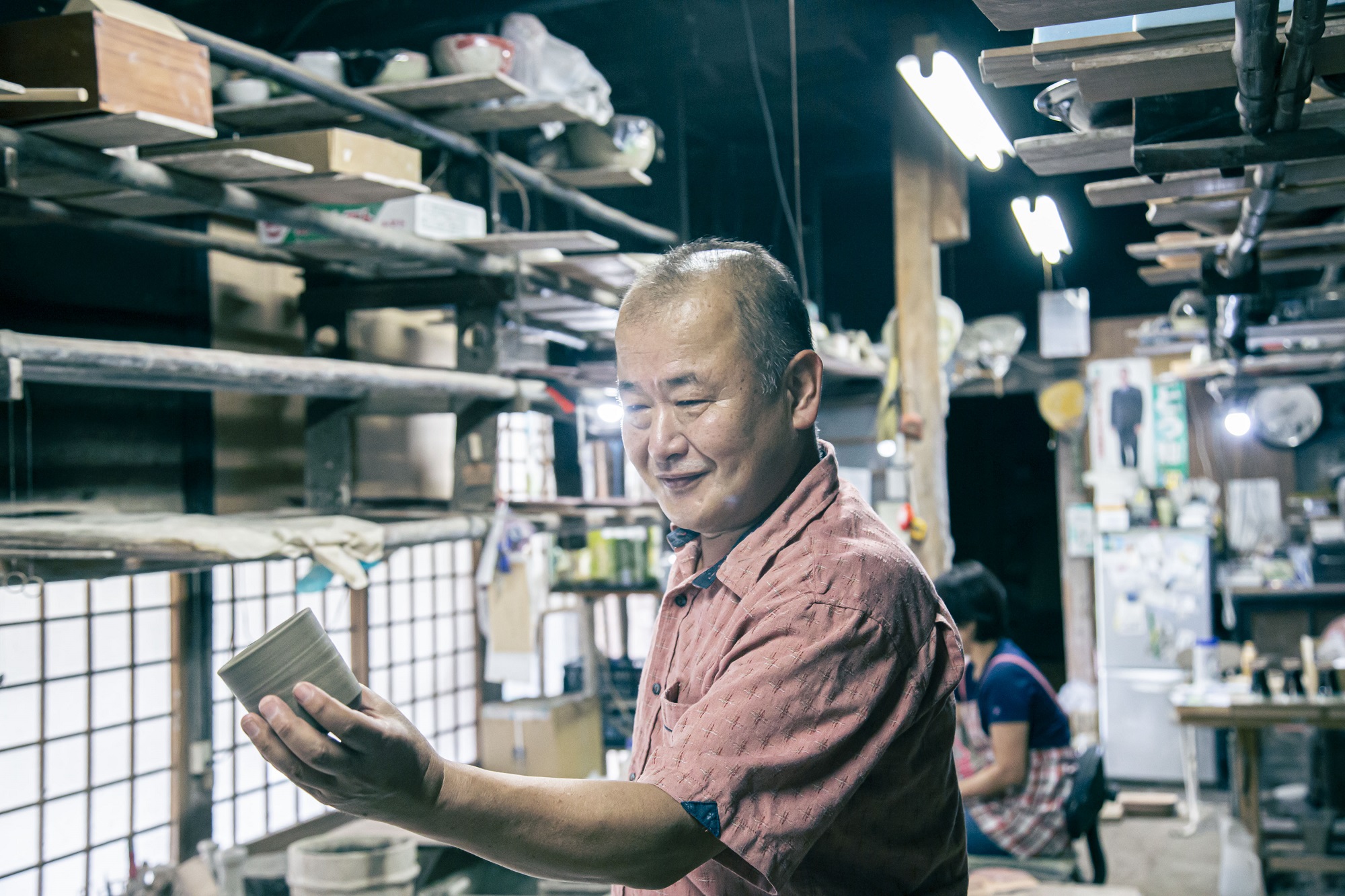
―――Did that experience allow you to finally become a professional potter?
Sakuma: That’s not the end of the story. Making the right shape is just the beginning when it comes to pottery. It is also important to apply the glaze in a manner that showcases our kiln’s original coloring style. What the craftsman taught me was to make an approximation using the ladle. As the glaze is made of natural raw materials, it is impossible to know precisely how much of each component it contains as the ratio of the components changes every time. The process of firing the clay, checking the result, and making fine adjustments over and over again so that I could gradually approach the ideal color is not easy at all. To be honest, I have yet to create a perfect color that I am 100% satisfied with, but I think I am around 90% of the way there. However, the fact that I haven’t found the perfect color is probably why I am able to continue working on it.
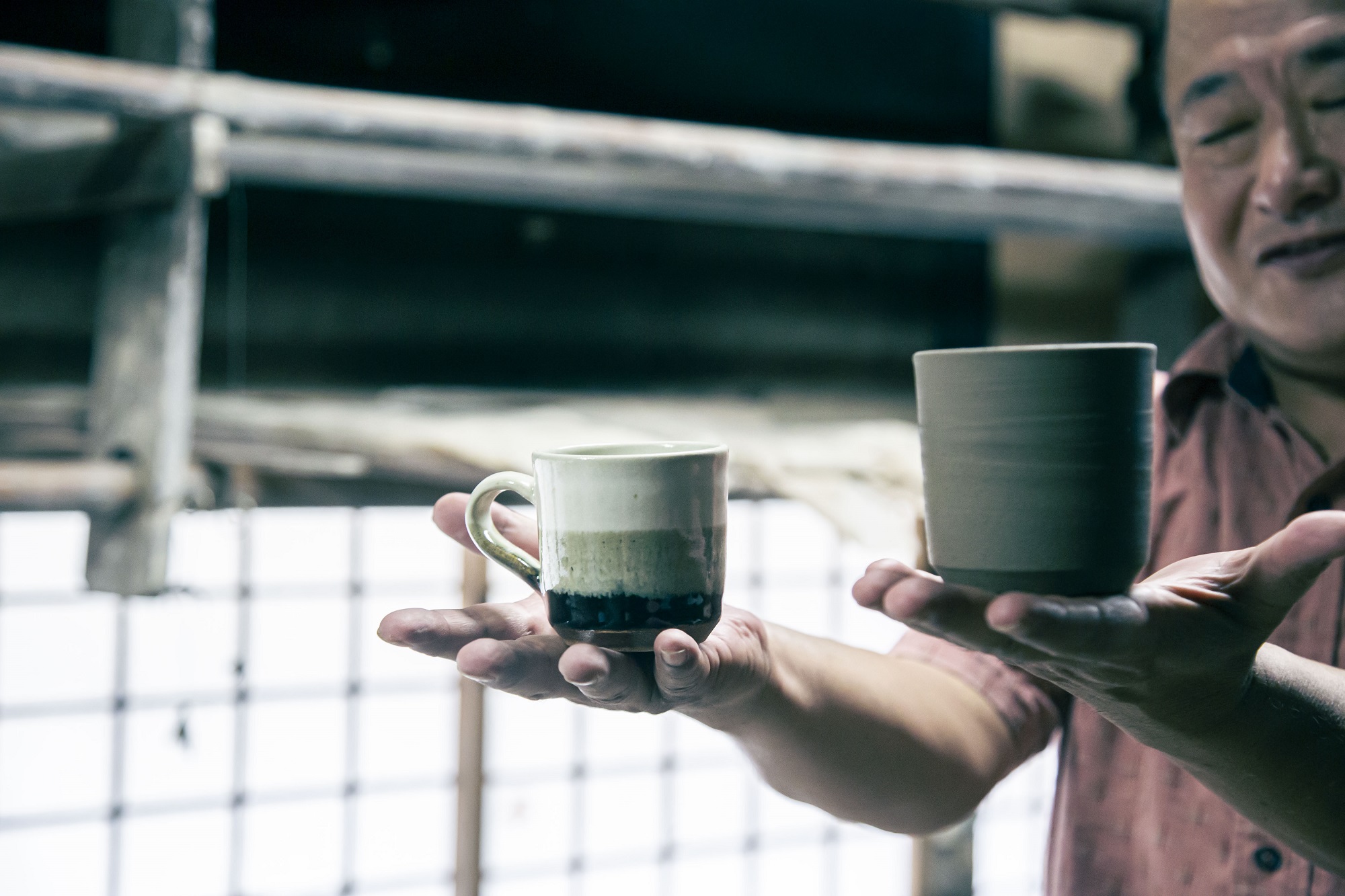
―――Not many people know about the glaze used in Mashiko ware. Can you tell us more about it?
Sakuma: There are five major kinds of glaze used in Mashiko ware.
・”Kakiyu” is a glaze made exclusively from powdered Ashinuma stone. It takes on a subdued and elegant brown color when fired.
・”Nukajiroyu” is a glaze made from the ashes of burned rice husks. It takes on a white color when fired.
・”Seijiyu” is a glaze made by adding copper to “Nukajiroyu.” It takes on a deep and stunning blue color when fired.
・”Namijiroyu” is a glaze that is primarily made from Oyatsu sand and limestone. It turns transparent when fired.
・”Honguroyu” is a glaze that contains a high concentration of iron. It takes on a black color when fired.
It is probably a good idea to keep these five kinds of glaze in mind.
―――I see. I never knew there were so many different kinds of glaze. How long has Mashiko ware been around?
Sakuma: Mashiko is regarded as a traditional industrial area in Japan. An area needs to have over 100 years of history to be designated as such. Mashiko has a long history that is said to have begun back in 1854.
There was a high demand for Mashiko ware in Tokyo, which was called Edo at that time. There were two main reasons for the popularity of Mashiko ware. There was no courier service back in those days, and it was time-consuming for people to transport heavy and fragile water bottles and mortars, which are prone to breakage, over 100 km by cart. How did they transport these items in the end? They used the rivers. The Kinugawa River runs through Moka, the neighboring city of Mashiko. From Kinugawa River, the pottery was then transported to Edo via Tone River, Tone Canal, and Edo River.
Another reason for the popularity of Mashiko ware was the abundance of raw materials such as clay and pine wood, which is used in the glaze and as fuel, in the mountains behind Mashiko. It was extremely difficult in those days to transport such materials over long distances. Since these materials could be sourced from the mountains nearby, they were inexpensive to transport and could be used to make large quantities of Mashiko ware.
The combination of these two factors led to the rise of Mashiko ware.
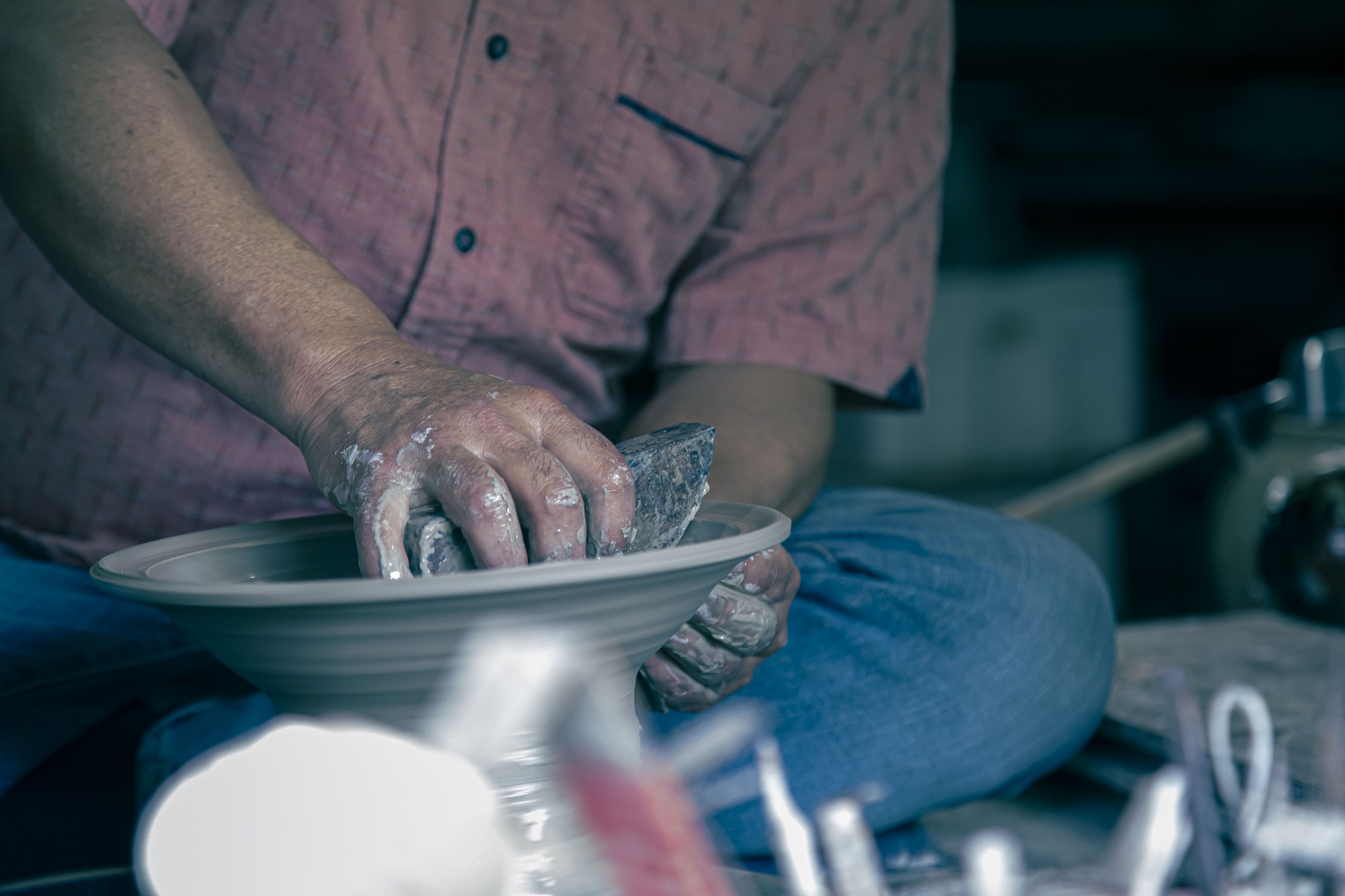
―――That explains the popularity of Mashiko ware. What kind of activities are you involved in these days?
Sakuma: I hold solo exhibitions in Tokyo and Mashiko several times a year, so I make every effort to create original works for these exhibitions. Of course, I also create items based on orders that I take from retailers with whom I have a working relationship. I make batches of the same item for these orders I receive from retailers, but for solo exhibitions, I need to make works that are unique. I usually go to my potter’s wheel late at night when everyone is asleep so that I can concentrate on what I am working on. Either way, when I am making these items, I always consider the perspective of my customers who purchase and use them. In fact, I often imagine how my customers would use these items when I am making them. But of course, it is the customer who ultimately decides how they wish to use the product. Even something that is originally intended as tableware can be used as a vase. I am delighted when people use the items I make in creative ways.
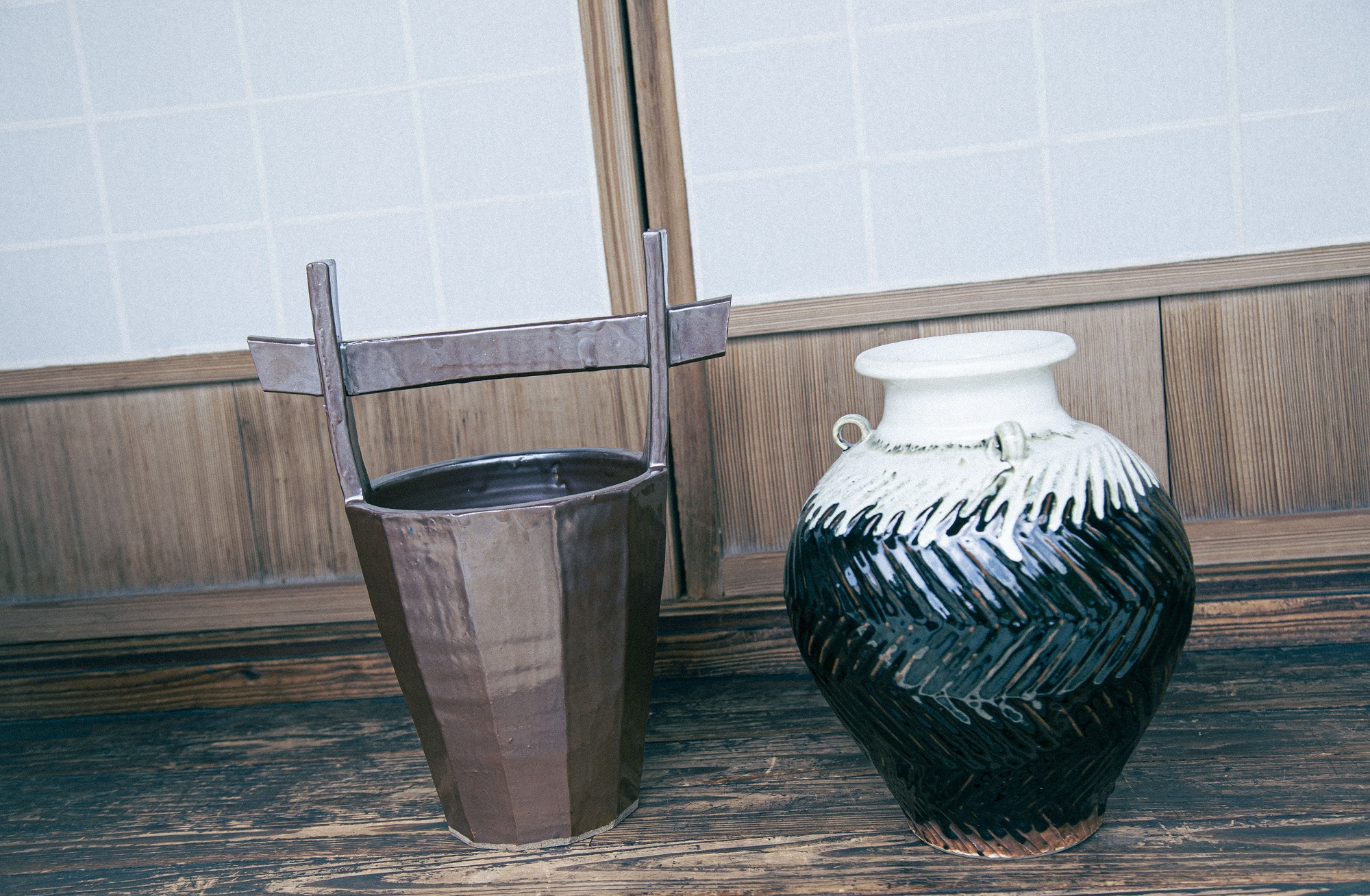
―――In other words, Mashiko ware can be used in many different ways?
Sakuma: That’s right. Mashiko has always been a production area that encourages the autonomy of craftsmen. There is no restriction on what we can or should make, or what we are prohibited from making. We can make whatever we want.
It also doesn’t matter whether someone was born in Mashiko or came from elsewhere. As long as the pottery they are making is historically considered Mashiko ware or modern pottery, we can all work together.
Shoji Hamada-sensei, who was responsible for raising public awareness of Mashiko ware, had come to Mashiko from Kanagawa Prefecture before he produced many creative and original works. Until then, Mashiko ware was associated with everyday tableware, and it was something that would be stored away in the corners of a kitchen. Shoji Hamada-sensei’s arrival in Mashiko elevated Mashiko ware to something that people would display in their alcove. If Hamada-sensei had been told, “We don’t accept outsiders here,” we might not have the Mashiko ware brand as we know it today. This open-minded culture is one of the best things about Mashiko. It is even possible for international artists to relocate to Mashiko and pursue their activities here. Today, there are over 200 potters and ceramic artists who have moved to the Mashiko area and are working here. If we look at the larger area around Mashiko, this number rises to over 400. To be honest, there is no other area like this anywhere else in Japan (laughs).
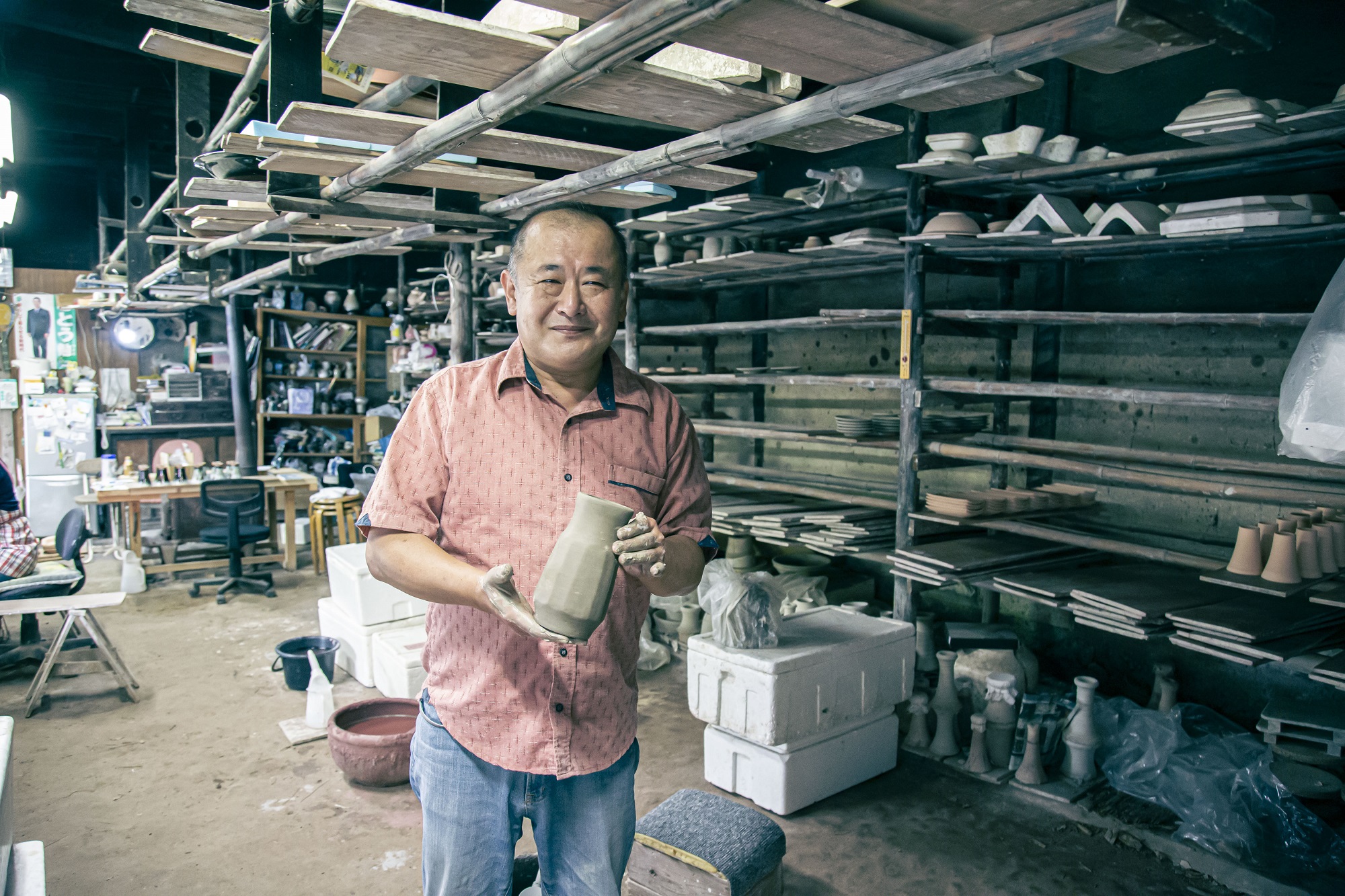
Profile
1963: Born in Mashiko as the eldest son of Kenji Sakuma and the grandson of Totaro Sakuma
1985: Graduated from the School of Art, Nagoya University of Arts
1986: Trained at Tochigi Prefectural Ceramic Training Institute
Started living with Totaro Sakuma
1996: Produced works for clients ranging from the Nikko Toshogu shrine to the Leeds Royal Armories Museum
Produced matcha bowls donated to the new “Fukutoku-an” building
1999: Nominated for the 73rd Kokuten Exhibition and exhibitions in subsequent years
2002: Awarded Honorable Mention at the 76th Kokuten Exhibition
2003: Awarded the Newcomer’s Prize at the 77th Kokuten Exhibition
2005: Awarded the Kokuga Award at the 79th Kokuten Exhibition and nominated as an associate member of the Kokuga Society
2006: Awarded the Minister of Economy, Trade and Industry Encouragement Prize
2007: Works collected at the Mashiko Museum of Ceramic Art
2012: Served on the judging panel for the art exhibition at the Tochigi Prefectural Art Festival
2013: Appointed as a technical advisor for the art exhibition at the Tochigi Prefectural Art Festival
Appointed chairman of the Mashiko Pottery Cooperative Association
2014: Nominated as a member of the Kokuga Society
Produced commemorative souvenirs for honorary residents of Tochigi Prefecture
2016: Works collected at the Nikko Toshogu shrine
2017: Awarded the Director-General’s Special Achievement Award by the Kanto Bureau of Economy, Trade and Industry
Fujiya Sakuma continues to hold solo and group exhibitions every year in Tokyo, Utsunomiya, and Mashiko.
〒321-4217, Mashiko 644-2, Mashiko-machi, Haga-gun, Tochigi
For inquiries to potters, please contact the following email address
For inquiries to artists, please contact the following email address